Techno logies
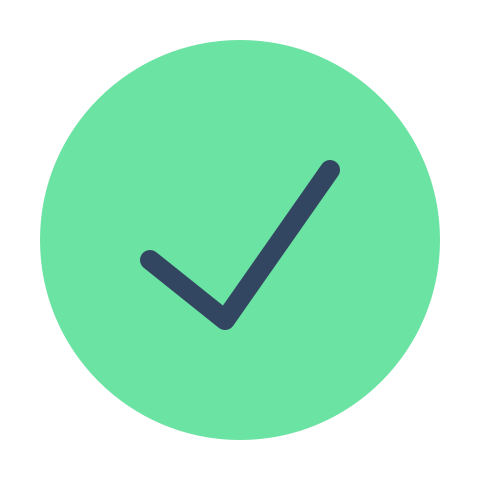
Deep Draw Metal Stampings
Deep-draw stamping is a high-speed, high-value shape transformation process in which sheet metal is drawn into a forming...
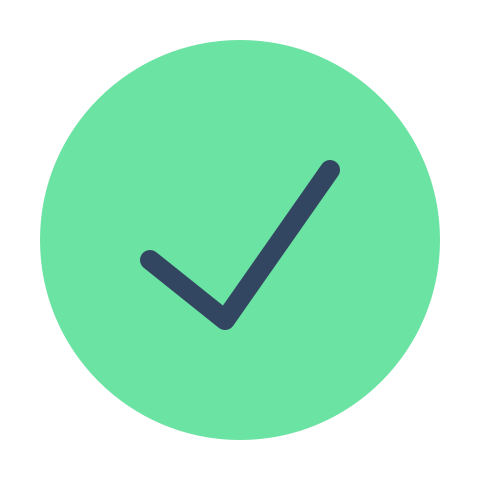
Progressive Die Stamping
In progressive die stamping, an automatic feeding system pushes the strip of metal through all of the stations of the stamping...
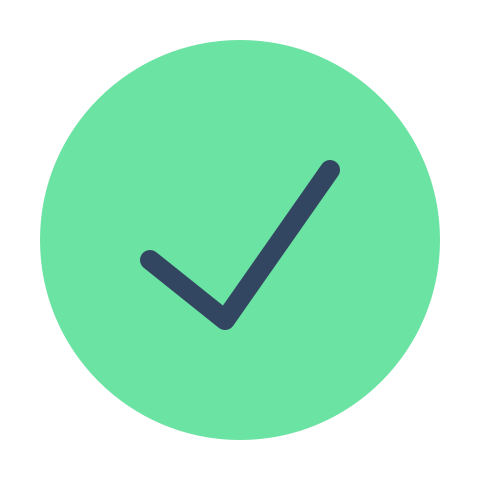
Assembly
The assembly process brings together design, manufacturing and logistics to create a multi-piece product with...
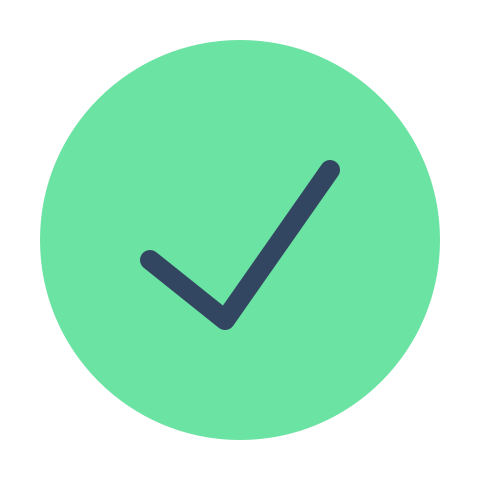
Simulation and Product Engineering
The JMS Engineering team utilizes DEFORM® simulation software...